Дополнительные компоненты для красок Marabu
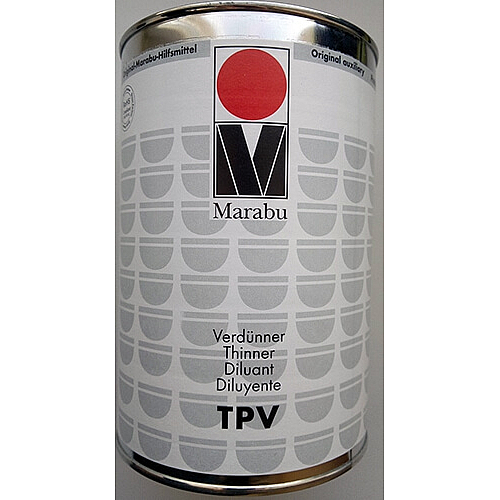
Разбавитель Marabu PLV, 5 л
Очиститель Marabu PLR, 5 л
Разбавитель Marabu 7037, 5 л
Замедлитель Marabu SV1, 5л
Замедлитель Marabu SV9, 5 л
Назначение и применение дополнительных компонентов Marabu для трафаретных и тампонных красок.
В данной статье приводятся описания и свойства, области применения и преимуществ использования дополнительной химии.
При добавлении в краску дополнительных компонентов крайне важно соблюдать точность пропорций или рекомендаций по количеству добавки, поэтому настоятельно рекомендуется использовать электронные весы. Рекомендации по количеству добавок, относятся для каждой отдельной серии краски.
ЗАМЕЧАНИЕ
Следует понимать, что любой дополнительный компонент, который добавляется в краску, изменяет её характеристики. По этой причине, перед тем как печатать основной тираж, настоятельно рекомендуется произвести тестовую печать для проверки.
ВАЖНО!
Количество добавки, которое рекомендовано к добавлению в краску, указано в весовых мерах, а не в объемных единицах!
ПРЕДОСТЕРЕЖЕНИЯ
Дабавка применённая в большем объёме, чаще всего негативно влияет на качество печати и может вызывать различные проблемы, такие как, уменьшение степени адгезии к материалу или повышенное растекание краски.
ВЯЗКОСТЬ
Под вязкостью понимается насколько жидкой или густой является краска, и как это можно регулировать. Перед началом печати крайне важно довести краску до состояния нужной степени вязкости, так как этот параметр влияет на растекаемость краски, пограничную четкость отпечатков, размер открытой ячейки сетки, а также сказывается на поведении краски при сушке и её длительности, на выбор скорости печати и, в некоторых случаях, на адгезии самой краски. Поскольку оборудование можно настроить по разному и на разные скорости печати, краски не поставляются готовыми к работе. Перед началом печати вязкость краски необходимо отрегулировать путем добавления разбавителя.
Количество разбавителя, рекомендуемое при различных видах работ.
10-15% Для однокомпонентной краски при печати «плашки» на ручном оборудовании и на плоскопечатных станках.
15-20% Для однокомпонентной краски при печати на цилиндрическом автомате.
10% Для однокомпонентной краски при полноцветной печати на ручном оборудовании и на плоскопечатных станках.
15% Для однокомпонентной краски при полноцветной печати на цилиндрическом автомате.
10% Для двухкомпонентной краски (с отвердителем) при печати «плашки» на ручном оборудовании и на плоскопечатных станках.
5% Для двухкомпонентной краски (с отвердителем) при полноцветной печати на ручном оборудовании и плоскопечатных станках.
Все цвета каждого вида краски следует проверять на корректную вязкость как перед печатью, так и в процессе печати. Следует помнить о двух исключениях.
Кроющая белая краска любой серии всегда более густая, чем все остальные цвета, из-за повышенного содержания пигмента.
Краски для полноцветной печати более густые, чем стандартные кроющие, поэтому напечатанная точка растра хорошо ложится на запечатываемый материал и не растекается.
Разбавители
Добавление разбавителя в краску оказывает прямое влияние на степень вязкости, текучести, размера открытой ячейки сетки, скорость высыхания, стойкость к слипанию отпечатков, на поведение связующей базы краски и, главное на адгезию краски к поверхности нанесения. Поскольку разбавитель уже включён в состав краски при изготовлении, их совместимость гарантирована. Все серии красок Marabu невозможно разбавлять одним или двумя универсальными разбавителями. Для разных серий красок и специальных условий использования существует 13 различных разбавителей.
Для правильного подбора разбавителя к конкретной краске следует сверяться с листами технического информации, маркировкой на банке краски и картой смешения.
Разбавители для распыления краски:
Если краска наносится путем распыления (с помощью краскопульта), рекомендуется использовать очень быстро испаряющиеся разбавитель. Основным показателем этого является способность краски очень быстро высыхать на поверхности нанесения, чтобы добиться ровного красочного слоя.
Замедлители
Замедлители – это, по сути, такие же сольвенты, как и разбавители, но имеющие значительно более низкий уровень испарения. Хотя замедлители и улучшают такой показатель, как размер открытого пространства ячейки сетки, они заметно увеличивают время высыхания краски, и соответственно снижают стойкость к слипанию отпечатков (в стопе). Замедлители обычно применяют в сочетании с разбавителем при печати тонких деталей или полноцветных изображений, или если работа ведется на медленных скоростях печати. Стоит помнить о том, что замедлители также оказывают влияние на вязкость краски как и разбавители, поэтому выбираются по принципу совместимости с краской и сохранению хорошей адгезии в комбинации с разбавителями.
В тампопечати замедлитель играет важную роли в регулировании скорости подсыхания слоя краски для создания хорошей адгкзии к печатному тампону и окрашиваемому материалу.
Резюме
Любой разбавитель или замедлитель состоит из смеси сольвентов и влияют на скорость испарения из краски, что является важным показателем. Разбавители испаряются быстрее, чем замедлители.
Разбавители ассортимент:
Скорость испарения |
Способность растворения |
Температура вспышки |
Запах |
Категория класса опасности |
|
GVL |
медленная |
хорошая |
72 C |
слабый |
Xn |
LIGV |
медленная |
хорошая |
40 C |
слабый |
Xi |
MMV |
быстрая |
низкая |
34 C |
слабый |
Xn |
PLV |
Более быстрая |
хорошая |
36 C |
слабый |
Xi |
PSV |
Более быстрая |
низкая |
32 C |
слабый |
Отсутствует |
PUV |
Более быстрая |
хорошая |
47 C |
средний |
Xi |
PV |
медленная |
хорошая |
72 C |
слабый |
Xn |
QNV |
медленная |
хорошая |
47 C |
средний |
Xn |
SPV |
средняя |
хорошая |
46 C |
средний |
Xn |
UKV1 |
Очень быстрая |
Очень хорошая |
43 C |
сильный |
Xn |
UKV2 |
быстрая |
хорошая |
49 C |
средний |
Xn |
UR3 |
Очень быстрая |
хорошая |
42 C |
средний |
Xn |
YV |
медленная |
Удовлетворит |
50 C |
средний |
Xn |
Разбавители в виде спреев
Скорость испарения |
Способность растворения |
Температура вспышки |
Запах |
Категория класса опасности |
|
PSV |
быстрая |
низкая |
32 C |
слабый |
Отсутствует |
TPV |
быстрая |
хорошая |
44 C |
слабый |
Xi |
7037 |
Очень быстрая |
Очень хорошая |
-4 С |
сильный |
Xi, F |
Замедлители
Скорость испарения |
Способность растворения |
Температура вспышки |
Запах |
Категория класса опасности |
|
SV1 |
средняя |
хорошая |
82 C |
слабый |
Xi |
SV3 |
Медленная |
низкая |
91 C |
слабый |
Xn |
SVS 1) |
быстрая |
Очень хорошая |
81 C |
сильный |
Xn |
SVS 2) |
быстрая |
Очень хорошая |
77 C |
слабый |
Xn |
SV9 |
медленная |
низкая |
102 C |
слабый |
Отсутствует |
SV1 0 |
средняя |
хорошая |
74 C |
слабый |
Xn |
Очистители форм
Скорость испарения |
Способность растворения |
Температура вспышки |
Запах |
Категория класса опасности |
|
PLR |
быстрая |
низкая |
15 C |
Средний |
Xi, F |
UR3 |
быстрая |
хорошая |
42 C |
слабый |
Xn |
Xi – раздражающее воздействие. Xn – вредное воздействие. F – высокая воспламеняемость
Примечание
Данные, указанные в графе «скорость испарения», получены из пропорций, составленных для основных сольвентов. Этот показатель можно назвать теоретическим, поскольку не принималось во внимание взаимное влияние сольвентов при их смешивании, а также влияние связующих продуктов. В действительности, не следует думать, что высокий показатель скорости испарения автоматически обеспечивает качественное состояние открытых ячеек сетки. Скорость испарения является, на самом деле, лишь условным параметром, и, поэтому, должна всегда контролироваться на практике.
Что касается категории класса опасности, то данные, приводимые в этой графе, вовсе не заменяют ту полную и современную информацию, которая детально приводится о продукте в технических листах и на маркировке самой емкости. Данные в колонке «Запах» являются субъективным показателем, поэтому каждый может оценивать эту характеристику продукта по-разному, в зависимости от индивидуальных особенностей.
Общие рекомендации
Поверхность полистирола не является стойкой к растворителям, поэтому позволяет проникать растворителю внутрь материала весьма быстро. Для очистки полистирола мы рекомендуем пользоваться разбавителем PSV, отличающимся слабым запахом и быстрой скорость испарения.
Элементы из литьевого пластика, имеющие высокое внутреннее напряжение, также требуется обрабатывать слабым растворителем, чтобы получить хорошие печатные свойства. Рекомендуется растворитель PSV.
Прозрачные базы
Практически все серии красок имеют в своем ассортименте прозрачную базу (D 409, GL 409, GN 409, GO 409, GR 409, LIG 409, LIP 409, LIS 409, MM 409, MS 409, P 409, SL 409, SR 409) для следующих основных целей:
- Для уменьшения насыщенности цвета краски при полноцветной печати.
- Для увеличения вязкости краски как кроющих, так и процессных цветов.
- Для уменьшения текучести краски обычных кроющих цветов при печати тонких деталей или при печати с негативных изображений.
Прозрачные базы всегда включают исходное связующее вещество соответствующей серии краски и, поэтому, всегда сочетаемы с любым цветом. При их изготовлении добавляются специальные загустители, поэтому внесение 5-20% прозрачной базы в любой цвет уменьшает способность краски к растеканию и, в то же время, увеличивает ее вязкость. Чтобы получить полное смешение краски с прозрачной базой, мы рекомендуем добавлять разбавитель и/или замедлитель сначала в прозрачную базу, а затем все вместе непосредственно в краску.
Преимущества
- Увеличение тиксотропности, текучесть краски при этом уменьшается.
- Возрастании вязкости.
- Оптимальная сочетаемость.
- Стандартный продукт.
- Возможность добавления вручную, простота использования.
Недостатки
- Уменьшение кроющей способности краски.
- Некоторое уменьшение степени глянца отпечатка.
- Возможное уменьшение пригодности к дальнейшему формованию изделия.
- Наличие в большинстве, (но не во всех), сериях красок.
- Уменьшение стойкости изделия к погодным условиям.
- Небольшое уменьшение степени гомогенности краски.
- Уменьшение яркости краски, в зависимости от процента добавленной базы.
ТИКСОТРОПНОСТЬ
Характерный для краски термин «реология» описывает такое её свойство, как текучесть, (склонность к растеканию) и зависит как от связующего вещества, так и от компонентов, используемых для разбавления.
Мы различаем краску по двум основным типам. «Короткий» означает, что краска имеет высокую тиксотропность (плохую способность к растеканию) и слабые внутренние связи. Струя краски очень быстро обрывается при наливании ее на шпатель из банки. «Длинная» краска означает низкую вязкость (хорошую способность к растеканию) и сильные внутренние связи, которые удерживают краску длительное время как единое целое. Такая характеристика поведения краски, как текучесть, наравне с прочими параметрами, (например, с содержанием твердой составляющей), оказывает существенное влияние на перенос краски с формы на поверхность нанесения. Кроме того, она влияет на способность к дальнейшему формованию отпечатков, на поведение краски на материалах со статическим электрическим зарядом, на размер открытой ячейки сетки и на пограничную четкость тонких деталей, а также на качество полноцветной печати. Любая серия краски в действительности разрабатывается для определенного применения, поэтому реологические свойства краски известны заранее. Однако их можно корректировать путем добавления соответствующих вспомогательных продуктов. Преимуществом красок с большой вязкостью является повышенная химическая стойкость, которая обеспечивается за счет выбора подходящего связующего.
Загуститель STM
Загуститель STM в виде порошка существенно увеличивает вязкость и тиксотропность печатной краски (с понижением ее текучести), если добавить его в количестве 1 – 2 % и перемешать в миксере. Эта добавка абсолютно необходима при печати тонких деталей с позитивных и негативных изображений, рельефных дизайнов, (если требуется получить толстый слой краски), и при печати на пористых материалах с большой абсорбцией (например, на рыхлой бумаге).
Преимущества
- Краски не «проваливаются» в материал.
- Вязкость увеличивается.
- Насыщенность (плотность цвета) краски не уменьшается.
- Универсальное использование.
Недостатки
- Необходимо перемешивание краски с помощью миксера.
- Способность к формованию отпечатков значительно снижается.
- Уменьшается стойкость к погодным условиям.
- Степень глянца снижается.
- Уровень растекания краски не является оптимальным.
Замедляющие пасты VP, MSVP
Паста VP хорошо подходит для печати очень тонких деталей, а также для полноцветной печати. Добавление ее в количестве 10 – 15 % дополнительно к растворителю и/или замедлителю сохраняет вязкость краски достаточно высокой, с удовлетворительным коэффициентом открытой ячейки сетки. Такая паста может быть добавлена в большинство красок на основе растворителей, за исключением серий GL, P, PP, PU и PY. Для серии Marasoft MS предлагается специальная замедляющая паста MSVP.
Антистатическая паста AP
Паста AP, первоначально разработанная для тампонных красок, также может применяться и в трафаретной печати. Паста в качестве наполнителя уменьшает «жесткость» краски, то есть, ее текучесть при добавлении 10 – 15% увеличивается. Это приводит к улучшению качества печати тонких деталей, и краска становится при этом менее чувствительной к статическому электричеству.
Краткий обзор
Пояснение. ↑ = увеличение ≥ = незначительное увеличение
→ = неизменное состояние
↓ = уменьшение ≤ = незначительное уменьшение
Добавка |
STM |
VP |
AP |
Физическое состояние и количество |
Порошок 1 – 2 % |
Паста 10 – 15 % |
Паста 10 – 15 % |
Вязкость |
↑ |
→ |
≥ |
Тиксотропность |
↑ |
≥ |
↑ |
Укрывистость |
→ |
↓ |
↓ |
Растекаемость |
↓ |
→ |
→ |
Степень глянца |
↓ |
≤ |
↓ |
Замечания |
Размешивание миксером |
Увеличивается размер открытой ячейки сетки |
Минимизируются проблемы со статическим зарядом |
МАТИРОВАНИЕ
Сильный глянец краски может быть значительно уменьшен, благодаря добавлению вспомогательных продуктов. Матирующие пасты ABM, MSM, PUM.
При добавлении в краску от 10% до 30% универсальной матирующей пасты ABM, степень глянца снижается в соответствующей пропорции. Как следствие этого, увеличивается шероховатость красочного слоя, что приводит к уменьшению отражения падающего света, и, соответственно, к появлению матового оттенка. В зависимости от количества добавленной матирующей пасты ABM, укрывистость и стойкость к истиранию отпечатков может снизится. Для серий Marasoft MS и Marapur PU имеется две специальные матирующие пасты (MSM и PUM), с теми же технологическими свойствами.
В общем случае, для двухкомпонентной краски (с отвердителем), например, Marapur PU, матирующую пасту следует добавлять в уже готовую к печати смесь краска/отвердитель так, чтобы пропорция краска/отвердитель не была нарушена. Поскольку степень глянца таких цветов, как белый/кроющий белый всегда слабее, как правило, остальных оттенков, количество матирующей пасты должно быть снижено до 10% - 20%. Для серии Glass Ink GL мы вообще не рекомендуем применять пасту ABM, только порошок MP может быть использован.
Матирующий порошок MP
Если напечатанная краска должна обладать матовой поверхностью, не теряя при этом хорошую адгезию, следует воспользоваться универсальным матирующим порошком MP. Рекомендуется добавка от 1% до 4% (максимум 2% для белого цвета). В этом случае порошок нужно примешивать в краску с помощью миксера. Порошок MP в действительности является сырьевым материалом, не содержащим ни какого связующего. Поэтому, он идеально подходит для всех серий красок, включая и двухкомпонентные.
СТОЙКОСТЬ К ПЛАСТИФИКАТОРАМ
Мягкий ПВХ сильно насыщен добавками пластификатора, который находится в свободном состоянии внутри материала (10 – 40%) и может впоследствии мигрировать в красочный слой после завершения печати. Хорошие краски для мягкого ПВХ имеют способность «связывать» пластификатор в красочной пленке, сохраняя при этом хорошую устойчивость к слипанию отпечатков и адгезию с запечатываемой поверхностью. Для повышения эффективности данного процесса в краску можно добавить 10 – 30% матирующей пасты (ABM, MSM или PUM) или матирующего порошка MP, как описано выше. Оба эти способа дают возможность получить шероховатую поверхность красочного слоя с маленькими углублениями, в которые может проникнуть пластификатор, независимо от его количества в пластике. Добавление паст ABM или MP снижает степень глянца и, одновременно, абразивную стойкость красочной пленки.
СТОЙКОСТЬ К СЛИПАНИЮ
Если трафаретные краски приобретают матовый оттенок за счет добавления матирующей пасты (10 – 30%) или матирующего порошка (1 – 4%), устойчивость к слипанию отпечатков в стопе заметно возрастает. Однако, степень глянца, как и абразивная стойкость (стойкость к истиранию) отпечатков при этом уменьшаются. Важно при этом контролировать, какие использовались разбавители и замедлители. Для хорошей устойчивости к слипанию не применяйте вспомогательные продукты с низкими скоростями испарения.
ЭЛАСТИЧНОСТЬ
Обычно слой напечатанной краски и тонкая поверхность нанесения (самоклеящаяся пленка) имеют разные коэффициенты расширения в процессе сушки или во время последующих термических нагрузок. Это приводит к тому, что в запечатанных листах появляется дополнительное напряжение, особенно, если после этого происходит резка или высекание прямо по красочному слою. В таких случаях следует соблюдать особую аккуратность.
Пластификатор WM1
Пластификатор WM1 в количестве 1 – 5% может быть добавлен в любую однокомпонентную систему (за исключением серии Maraprop PP). Это помогает «снять стресс и размягчить» напечатанную краску и минимизировать степень риска «закручивания углов» или усадки материала (самоклеящихся пленок). Пластификаторы – это исключительно слаболетучие вещества, которые сглаживают неэластичность связующего. При печати нескольких слоев краски на тонкой пленке (например, на двусторонних самоклеящихся пленках), пластификатор должен быть равномерно добавлен в каждый слой краски (в количестве 3 – 5%). Следует обязательно иметь в виду, что добавление пластификатора обязательно приведет к уменьшению скорости высыхания и, соответственно, к снижению устойчивости к слипанию отпечатков.
Контроль за остаточным растворителем
Если по окончании печати вы проводите резку или высекание отпечатков прямо по красочной пленке, важное значение, наряду с пластичностью используемого связующего и выбором пластификатора, имеет содержание остатков растворителя в печатной краске. Если процент растворителя слишком высок, поверхность и сама красочная пленка останутся недосушенными, в результате чего можно ожидать усадку материала или «закручивание углов» после резки или высекания. Вот почему, мы настоятельно рекомендуем использовать наиболее слабый замедлитель, проводить сушку только на стеллажах или в туннельной установке с теплым воздухом, и как можно большее время выдерживать отпечатанные листы перед последующими операциями.
РАСТЕКАНИЕ КРАСКИ
Большинство серий красок содержит специальные добавки в основной рецептуре для уменьшения поглощения пузырьков воздуха в процессе нанесения краски ракелем или при перемешивании в емкости. Дефекты «неровностей» часто появляются по причине слишком высокой вязкости краски, которую можно устранить путем добавления большего количества разбавителей. Если же эта мера не дает положительных результатов, можно воспользоваться следующими вспомогательными средствами:
Модификатор для печати ES (выравнивающая добавка)
Эта добавка на основе силикона (кремнийорганического соединения) уменьшает поверхностное натяжении краски и обладает пеногасительным свойством. Количество присадки не должно превышать 1%, в противном случае будут неизбежны проблемы с адгезией или повышенным напряжением в материале.
Модификаторы для печати VM1 и VM2
Обе разновидности модификаторов не содержат силикона (кремнийорганических соединений) и рекомендуются для таких серий красок, как Glass Ink GL (VM1) и Marapoly P (VM2) в том случае, если имеют место проблемы с выравниванием красочного слоя. Влияние этих модификаторов на другие серии красок настолько мало, что добавка простого разбавителя окажет если не лучшее, то, по крайней мере, и не худшее действие.
СТАТИЧЕСКОЕ ЭЛЕКТРИЧЕСТВО
При печати на пластиках, не имеющих полярности и чувствительных к статическому электричеству, таких, как полистирол PS, мы рекомендуем добавлять в краску 10 – 15% антистатической AP – пасты. Паста уменьшает «жесткость» печатной краски и при этом нейтрализует статическое электричество, благодаря присутствию полярных растворителей в своей рецептуре.
МОДИФИКАТОР АДГЕЗИИ
Полиолефины, например полипропилен, должны предварительно обрабатываться перед началом печати. Одна из возможностей для такой обработки – средство Primer P2.
Primer P2 - этот специальный сольвент наносится вручную по всей поверхности печати с помощью пистолета для распыления. Такая обработка позволяет проводить дальнейшую печать на полипропилене как однокомпонентной, так и двухкомпонентной краской. Эффективность обработки зависит от продолжительности действия сольвента, поэтому рекомендуется проводить нанесение не позднее, чем за 1 – 2 дня до печатного тиража.
В некоторых случаях оправдано внесение средства P2 непосредственно в краску Maraprop PP в количестве 5 - 10%.
ПРЕДВАРИТЕЛЬНАЯ ОЧИСТКА
Многие материалы, такие, как мягкий ПВХ или поверхности с порошковым покрытием, загрязнены невидимыми включениями или пластификаторами. Печать оказывается не удовлетворительной не только на самой поверхности, но и на внешней границе раздела, которая имеет плохую адгезию с краской.
Очиститель PLR
Использование данного очистителя на спиртовой основе позволяет удалять химические соединения на поверхности материала. Для этого можно просто протереть поверхность тряпкой, смоченной в очистителе для баннерных тканей, что часто заметно улучшает адгезию краски. Пожалуйста, не забывайте время от времени менять тряпку, иначе получится не предварительная очистка, а простое растирание грязи по материалу.
ОТВЕРДИТЕЛИ
Существуют такие серии красок, которые можно использовать и как однокомпонентные, и как двухкомпонентные. Для таких «смешанных типов» улучшить адгезию на трудных поверхностях, равно как химическую и механическую стойкость отпечатков, позволяет добавка отвердителя аналогичного тому, который добавляется в чисто двухкомпонентные краски. Важно иметь в виду, что работа с краской, в которую добавлен отвердитель, всегда лимитирована по времени (от 8 до 16 часов, за исключением отвердителя HT1). Для существующих серий красок, («отверждаемых» добавкой полиизоцианата), имеется три различных вида отвердителя.
Отвердитель H1
Отвердитель H1 – это алифатический полиизоцианат, не дающий пожелтения отпечатков при взаимодействии с краской и позволяющий получить довольно пластичную поверхностную пленку. Краска с добавленным отвердителем имеет относительно продолжительное «время чаши» (пригодна к работе) и характеризуется медленной скоростью полимеризации. Годится для наружного применения.
Отвердитель H2
Отвердитель H2 – это ароматический полиизоцианат, при добавлении которого в краску получается жесткая и прочная красочная пленка. Краска с отвердителем H2 быстро полимеризуется и имеет меньшее «время жизни», чем с отвердителем H1. Отвердитель H2 склонен к пожелтению при экспонировании УФ – светом (на солнечном свете при наружном применении). Это особенно заметно при добавлении его в кроющий лак, а также в белую краску или светлые цвета, смешанные с белым.
Отвердитель HT1
Это отвердитель, чувствительный к нагреву, который реагирует с основным связующим используемой краски. Принудительная сушка при температуре 150 С в течение 30 мин. позволяет использовать отвердитель HT1 вместо отвердителей H1 и H2, обеспечивая то же качество «отверждения» (полимеризации) краски. Большим преимуществом этого продукта является его длительное «время жизни» - до 6 месяцев!
Некоторые заметки по поводу отвердителей
В общем случае все отвердители очень чувствительны к сырости и повышенной влажности. Поэтому, процесс сушки отпечатков следует проводить в первые 24 часа в помещении с максимально возможно низкой влажностью. В противном случае частички отвердителя могут вступить в реакцию с водой, и эффективность присутствия отвердителя в краске пропадет. Хранение емкостей с отвердителем должно проходить в условиях абсолютно сухого воздуха. Банки должны быть всегда плотно закрыты после использования!
Более того, количество образованных молекулярных цепей (отвердителя со связующим), которые соответственно обеспечивают механическую и химическую стойкость напечатанной краски, значительным образом зависит от температуры, что свойственно всем двухкомпонентным системам. После проведения принудительной сушки краски при температуре 140 С в течение 20 – 30 мин. сразу же после завершения печати, вы добьетесь оптимального образования межмолекулярных связей (полимеризации красочного слоя) и, как следствие, великолепной устойчивости. Двухкомпонентные краски могут сохнуть и при комнатной температуре, но на образование межмолекулярных цепей может потребоваться до 7 дней, что не гарантирует, однако, такую же стойкость красочного слоя.
При печати на таких трудных поверхностях, как стекло, металл, термостатические пластики или на изделиях с повышенными требованиями эксплуатации (устойчивость к мытью в посудомоечной машине), принудительная сушка в печи совершенно необходима.
Отвердители GLH, YH и YH9
Названные отвердители разработаны специально для некоторых серий красок и, поэтому, не могут использоваться как универсальные.
GLH – отвердитель для серии по печати на стекле Ultraglass GL.
YH и YH9 – отвердители для серии Marapoxy Y.
РЕЗЮМЕ
Как правило, во все трафаретные краски включены необходимые добавки. Увлекаться модифицированием краски собственными силами не рекомендуется. Нам бы не хотелось заставлять вас превращаться в лаборанта или «загораться огнем экспериментатора» при прочтении вышеизложенной информации. Мы просто хотим объяснить вам, что в некоторых случаях модифицирование краски может быть полезным. Существует много возможностей позитивно повлиять на поведение краски, но можно также и существенно испортить ее.
По этой причине, использование вспомогательных продуктов и добавок должно проходить со знанием дела и полной ответственностью, проверяя свои действия с помощью электронных весов. Внесение добавок, в некоторых случаях, может оказать очень существенное влияние на свойства краски, поэтому пробное тестирование является абсолютно необходимым перед началом печатного тиража.